Heavy payloads and molten lead are no match for this heavy-duty robot helping to build industrial batteries. Neither is airborne lead dust, a health hazard for human workers.
When Battery Builders Inc. (BBI), a Naperville, Illinois-based manufacturer of industrial lead-acid batteries for lift trucks and other electric-operated equipment, decided to upgrade their facility, they got way more than expected from their new robot. They would more than double production with less labor, improve product quality, and reduce health and safety risks.
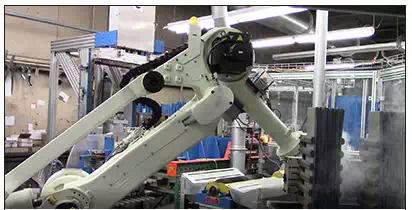
Frustrated by costly production delays caused by antiquated equipment, BBI worked with MAC Engineering from Benton Harbor, Michigan, to replace their 25-year-old COS (Cast-on-Strap) machine. MAC also integrated a Kawasaki ZX300S large payload robot to tend the new six-station COS machine. Automating the machine tending tasks reduced the number of workers from seven to five people and freed them up for more high-value tasks in other areas of the manufacturing facility.
The robotic process starts with the robot precisely aligning groups of vertically stacked battery plates, making sure the edges are even and flush. Then the robot picks up the plates and runs them over a large bristle brush to remove any lingering debris from the end connectors, or lugs. Next, the robot runs the product through a flux process, which prepares the metal lugs by removing metal oxides that could form beads when heated. The lugs are then dipped into tin to establish a stronger connection, and then dipped again into molten lead to connect the plates and establish the positive and negative posts. Finally, the robot places the battery plates into the last station, which automatically inserts the plates into a molded plastic casing.
BBI needed a precision workhorse to consistently align 136 kg of battery plates up to 500 times per day. The Kawasaki robot has a 300 kg payload and combines a long reach of 3230 mm with a minimal amount of dead space for a wide work envelope in a small footprint. High repeatability (±0.3 mm) makes it ideal for applications requiring precision and heavy lifting. Combined, these features enable the robot to reach multiple machines at varying heights, while generating a more consistent product.
“We have seen a visible change in product quality,” says BBI’s Assistant Manager. “It’s not only the robot that’s precise in its movements, it’s all of the equipment around it, too. Everything is automated together, and the combination makes for a more accurate product.”
During the multi-step COS process, the robot end-of-arm tooling only needs to change when the battery type is modified. When it’s time for a different battery type, an operator changes the gripper on the robot.
Higher Production, Lower Risk
Although increased production was BBI’s primary goal for the upgrade, the manufacturer experienced unforeseen health and safety benefits. Manually stacking the battery plates and loading them into cases generated more airborne lead dust and posed a greater risk for exposure than the new automated process. The old process also required employees to lift heavier loads, resulting in a greater risk of injury.
For BBI, it was important to see automation’s positive impact on not just their bottom line, but also on their employees’ work environment.
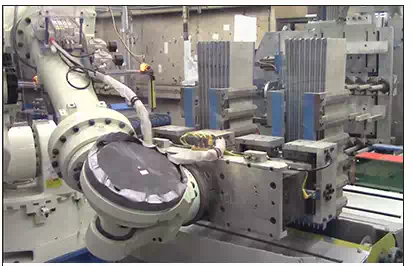
“We have seen significant drops in exposure air monitoring results and we anticipate lower blood lead levels over time from the reduction of airborne lead dust concentrations,” says BBI’s Environmental Health and Safety Specialist.
Any airborne lead dust that is created during the automated process is immediately captured by a local exhaust ventilation system and deposited in a HEPA-filtered dust collector. Any residual lead dust that collects on the robot’s surfaces is removed during BBI’s daily housekeeping routine with a HEPA-filtered vacuum and wet wipe-down. The Kawasaki ZX300S robot wrist and base are rated IP67 and IP65, respectively, and are dust tight.
Since replacing their old COS machine, BBI has experienced better, more consistent product quality using fewer worker hours. Employees who used to operate the old machine are now working in the battery assembly department, allowing BBI to focus more staff hours on the final stages of battery assembly and ultimately improve the overall quality of their batteries.
Automating the manufacturing process reduced the operators’ exposure to airborne lead dust and the amount of heavy lifting their roles require, resulting in a significantly safer work environment. Once all of the integration is complete, BBI expects to increase production from 400 to 1,000 battery cells per day – more than double their output before automation.
Robotic automation is taking on an ever-increasing role in the healthcare industry, too. Take the snake-like robots we explored in Robots and AI in the OR. They go where traditional surgical tools can’t. In the pharmacy, robots are going where humans shouldn’t.