Robots perform dull, monotonous jobs every day. Traditionally, this was their domain. But time, technology and experience has shown us they are capable of so much more. Productivity, quality and efficiency have moved to the forefront. ROI is now often measured in months, not years. Volume is not as critical.
With more focus placed on the gains, sometimes we forget what we save. The freedom from extreme temperatures, strenuous payloads, harsh chemicals and toxic fumes. Their uncanny ability to go where we can’t and perform jobs we shouldn’t. From chemical refining and hazardous material handling, to toxic drug compounding and subzero palletizing, the superhuman capabilities of robots take them to extremes.
Robotic Furnace Tapping
Furnace tapping is a grueling job. The heavy lifting is repetitive and physically demanding. Temperatures are hot enough to melt metal. Noxious fumes and toxic dust make the task especially unhospitable for humans. But for robots, and an experienced automation integrator, furnace tapping is no sweat.
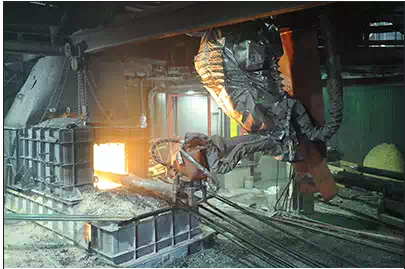
Founded in 1996, Specialized Analysis Engineering, Inc. (SAE) is an engineering services firm with expertise in industrial automation, robotics, process controls, systems integration, fabrication and wiring. The Logan, Utah-based firm has completed projects across a wide spectrum of industries including arc furnace tapping automation for phosphorus reduction furnaces and steel smelting furnaces.
SAE has automated six furnace tapping cells for a phosphate refining facility owned by pharmaceutical and agricultural giant Bayer. Located in Soda Springs, Idaho, the facility operates multiple electric arc furnaces to produce elemental phosphorus for herbicides.
During the refining process, a waste product is created in the form of molten slag that approaches 1650°C, hot enough to melt steel. This molten slag must be periodically removed from the furnace in a process called tapping. During the tapping process, the environment around the arc furnace is extremely harsh. Extreme high temperatures, the potential for splashing molten material, and noxious fumes and vapors make it hazardous for humans.
The operating environment is so extreme that even the robot needs protection. Under the metallic cover is a FANUC M-900iB/360 heavy payload robot inverted on a custom-built 7th axis positioner with coordinated motion. Inverted mounting allowed room for other activities in the workspace that would have been prohibited by a floor-mounted configuration.
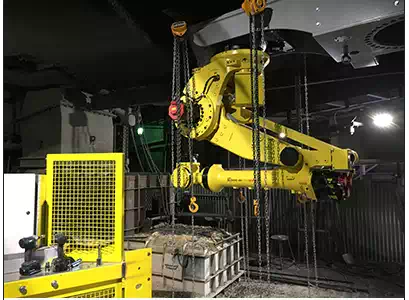
Takes the Heat, Lightens the Load
The robot must be able to operate in ambient temperatures that vary from -29°C during Idaho winters to over 38°C in the summer. To handle high ambient temperatures and the extreme process environment, the robot is protected by a heat-resistant Robosuit® made by RIA member Roboworld. SAE engineers worked directly with Roboworld to have their robot armor customized to accommodate the inverted mounting position and the accessory equipment required by this application.
SAE also equipped the robot with custom-built, thermostatically controlled, electrical-resistance heaters on all the joint motors and bearing housings to maintain operating capability during the extremely cold winter months. They also installed auxiliary insulation on the robot’s wiring harness beneath the protective suit. All the conduit and wiring in the electrical enclosures and operator panels in exposed locations were shielded and insulated for protection from the harsh operating environment.
Lane Nielson, SAE’s Engineering Manager, says that in addition to FANUC’s high level of accuracy and repeatability, the robot has proven robust enough to survive the very harsh operating environment near the furnace tap holes. With a 360 kg payload, it also has the required power to manipulate heavy tooling and perform demanding tasks 24 hours a day, 7 days a week.
The heavy tooling was custom designed and fabricated by SAE. Each robot end-of-arm tool is approximately 5.5 m long and weighs 113 kg. Four different tools are required for the robot to perform multiple functions during the furnace tapping process. The tools are stored in an automated tool rack. Tool changers made by RIA Platinum member ATI Industrial Automation are used to accurately locate each tool in the rack as it’s needed and automatically couple it to the robot arm.
The PLC control system built by SAE provides master control for the robotic cell, associated equipment, and safety system. It also interfaces with the customer’s SCADA system. A wireless remote pendant allows an operator to execute the system’s primary functions without remaining at a fixed location next to the control panel. The safety system comprises physical barricades, personnel access gates equipped with locking safety switches, E-stop pull cables, and E-stop buttons to protect people working around the robotic cell.
Prior to automation, this furnace tapping process was entirely manual. It required operators to have a certain level of strength and stamina to perform repetitive tasks with heavy and cumbersome tools. By integrating a robotic system, it creates job opportunities for people who would otherwise be physically incapable of performing the previously manual tasks. The robot is also able to manipulate tools that are much heavier, more robust, and have a longer lifespan than the previous manual tools used by human operators to perform the same work.

Comments are closed